近年来,湖北三宁化工股份有限公司围绕主产品附属物展开科研和废物利用,形成了一条闭合的循环产业链,每年可节约生产成本近4亿元。
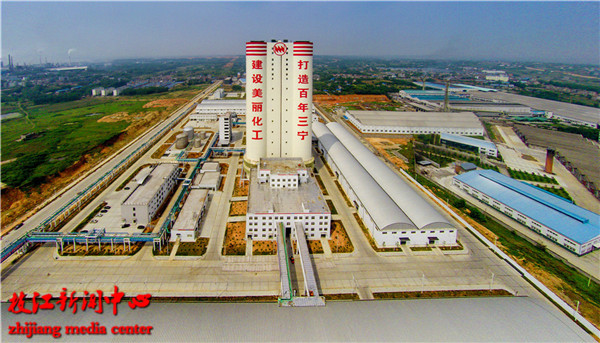
6月中旬,记者在湖北三宁化工股份有限公司看到,该公司生产的合成氨、氢气和硫酸等产品,源源不断传输到该公司己内酰胺生产基地,在这里合成己内酰胺。
据该公司现场技术人员介绍,生产己内酰胺所需的6大原材料,只有苯需要从外地采购,生产成本较同类装置降低20%左右,每年仅生产己内酰胺,原料费就可节约2亿多元。
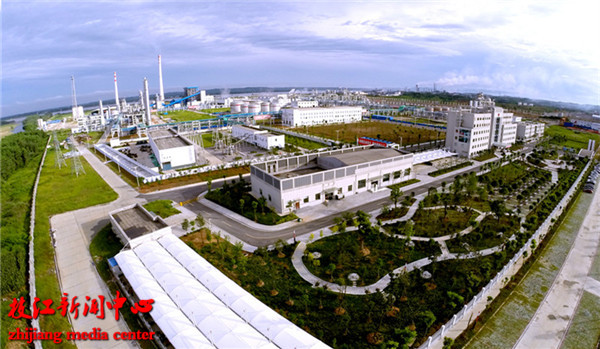
拉长产业链,形成产品链。近年来,湖北三宁化工股份有限公司围绕主产品附属物展开科研和废物利用,形成新的产品。目前该公司拥有合成氨、硫酸、磷酸、硝酸、双氧水、环己酮、氢气等基础原材料,基本上形成了一条闭合的循环产业链,废物都得到了有效利用。
循环利用能源和资源,使该公司每年节约电费近千万元,多年来保持在吨氨煤耗1069千克,吨氨电耗1223千瓦时,吨蒸汽耗量1120千克,合成氨制造成本1755元/吨,分别比行业平均水平低181千克、227千瓦时、180千克和245元/吨,节能降耗明显。
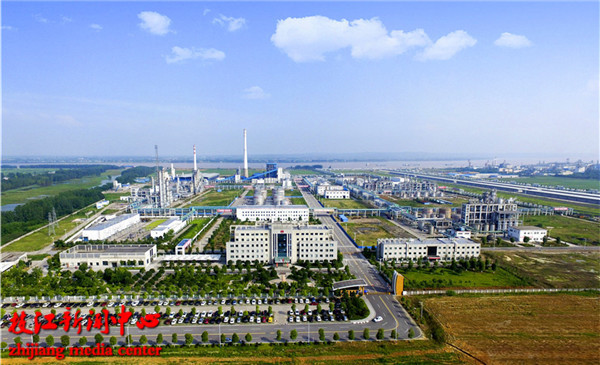
“化工企业走循环经济的路子,才是最终的发展方向。”湖北三宁化工股份有限公司董事长、总经理李万清说,由于该公司形成了闭合产业链,每年可节约生产成本近4亿元。在短短几年时间里,该公司销售收入翻了10倍多,利润翻了20多倍。